A cleaner, greener world starts from the ground up. Many commercial (as well as residential buildings have made green building practices like green building methods and the use of easily renewable or recycled building materials to get a jumpstart on applying green building practices to their projects. For those buildings already constructed, owners have decided to retrofit various fixtures or choose more green options when carrying out remodeling and renovation plans.
For years, we’ve been focused on cutting back consumption of electricity, fossil fuels, and other pollutants, but have seemed to neglect water consumption habits. Now, the industry is working toward including water consumption as a metric for building efficiency. Keep in mind, these strategies are not “set it and forget it” fixes for your water consumption and conservation goals.
Table of Contents
The Problem of Water Consumption
Water habits are easily controlled inside your home – not leaving the water running while brushing your teeth, turning the water off while soaping up during showers (or not taking long showers or baths), and more. During home renovations, you may install low-flow shower heads and toilets, and opt for water-saving appliances like dish washers and clothes washers. You may even install a tankless water heater to have hot water on demand rather than having to wait for it to warm up.
Commercial building can suffer from the same water inefficiencies as residential homes, but on a grander scale. Instead of a house with just three bathrooms, a dish washer and clothes washer, commercial buildings have rules and regulations regarding the number of bathrooms available as well as the number of stalls, urinals, and sinks that must be available. A two-story office building with two centrally located bathrooms already has at least four toilets. If individual office spaces also include bathrooms, the number skyrockets.
Specifically in Central Arizona’s arid desert climate, water usage and conservation is paramount when designing new buildings or the renovation of existing properties. Due to the area’s hot, dry, climate, the efficient use of water must be in the plans for any new build.
Solutions for Minimizing Your Building’s Water Consumption
In our article about retrofitting old spaces to meet modern needs, we spoke of the need for a thorough energy audit to find where your building is lacking and where small or large improvements need to be made to increase energy efficiency. The same is true when it comes to evaluating your building’s water consumption.
Water Audit
Also known as a water assessment, a water audit is an analysis of a building’s or business’ water usage. It helps identify inefficiencies and potential cost savings and documents the different ways to use water, when and how much water is typically consumed by the building, and identifies opportunities for reductions. The building’s water bills, and meter readings will help generate the most precise data regarding your building’s water consumption.

You can choose to conduct your own audit, or higher a professional. When doing a self-audit, you’ll have to track your company’s water usage over time and analyze the data yourself to identify inefficiencies and consider ways to make improvements. Professional audits are carried out by third-party experts specializing in evaluating water usage and developing conservation plans. Both will be beneficial and have the same goal (water efficiency), but a self-audit may miss things. A professional audit tends to be more comprehensive.
Low-Flow Plumbing Fixtures
Low-flow plumbing fixtures are synonymous with water conservation. Low-flow toilets, urinals, and sinks are often the first step businesses take when trying to increase water efficiency and conservation. If your building includes shower stalls or bath tubs – gyms, hotels, etc. – don’t forget to install low-flow shower heads and bath faucets.
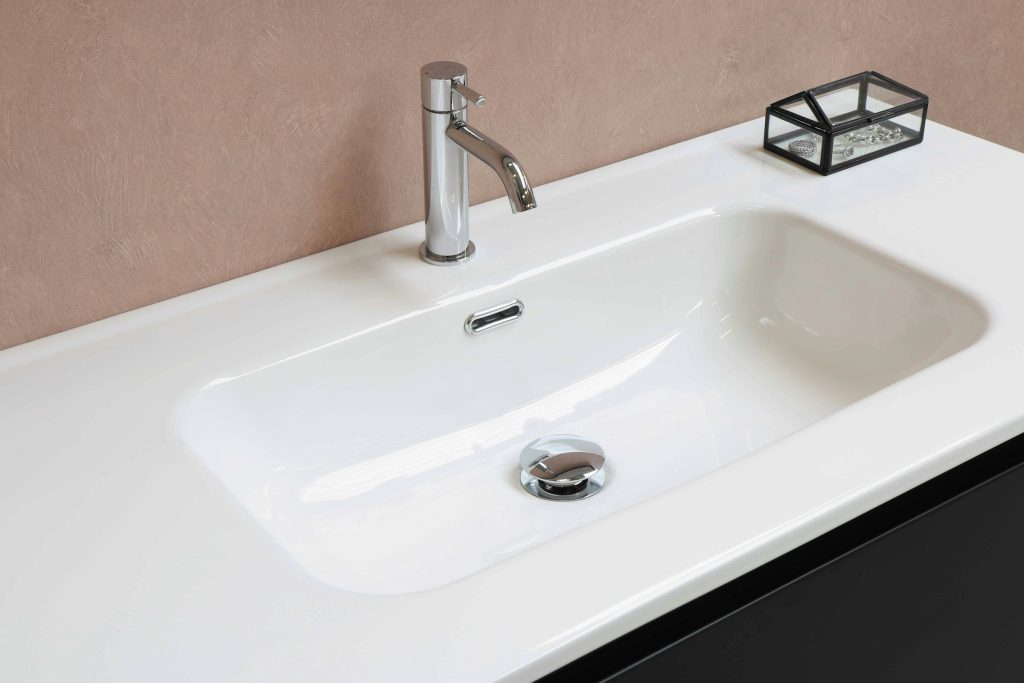
Things to consider when installing low-flow fixtures:
– Low-flow fixtures use less water but are not as effective as moving solids great distances along horizontal sanitary lines
– Employ methods to increase effectiveness and to avoid buildups and backups created by reduced water flow
– When retrofitting, pay close attention to the condition of the building’s type of pipe and pitch
– Less hot water flows through pipes of low-flow fixtures, resulting in waste due to the wait for hot water to reach faucets
– Low-flow fixtures require regular evaluation and maintenance for all water-conserving devices to make adjustments to flow-control devices (battery replacement in non-hard wired units, dirt/contaminate flushing, etc)
Gray Water
Reduce, reuse, recycle. It’s been the mantra for green living for decades. By reclaiming your building’s gray water (wastewater generated from water streams without fecal contamination, i.e., all streams except for the wastewater from toilets), you make the most of your building’s water supply.
Gray water is treated by a combination of solids separation, biological treatment, and ultraviolet disinfection. The system uses simple diversion from the main plumbing system for treatment via sand filters, aeration, electroflotation (removal of pollutants through generation of bubbles to collect and carry pollutants to the surface), and pressure filtration. The treated water is then stored in tanks. The treated and stored gray water can then be reused for toilet flushing, condenser water, and property irrigation. During the design process, it’s important to ensure your freshwater and gray water systems are piped separately, and the gray water system is specifically identified as a non-potable source.
Things to consider when installing a gray water reuse system:
– Gray water is no longer a source of potable water, meaning it’s not a source of drinking water, vegetation, or HVAC condensing water due to the chemicals involved in treatment.
– Gray water systems require significant design effort and initial costs
– Potential for contamination and pollution if mismanaged
– Post-installation running costs can be high for more sophisticated systems (but result in system payback for many years)
– Regular system maintenance of pumps, treating stations, and filters is needed
– Gray water systems are most cost-effective when the available gray water stays on par with demand
Rainwater Harvesting
In Arizona, rainy days are few and far between, barring monsoon season. In fact, Phoenix was deemed the #2 sunniest city in the U.S. in 2021 as reported by the National Oceanic and Atmospheric Association, with an average of 211 sunny days per year. It was beaten out only by Yuma.
The other 154 days of the year aren’t necessarily rainy, just not sunny. In making your building more water efficient, consider a rainwater harvesting system. Those stingy rainfalls are a prime source of free water – you just have to capture and treat it. These system are a viable option for when a building has a large roof area which also requires high demand for non-potable water (i.e., green roofs).
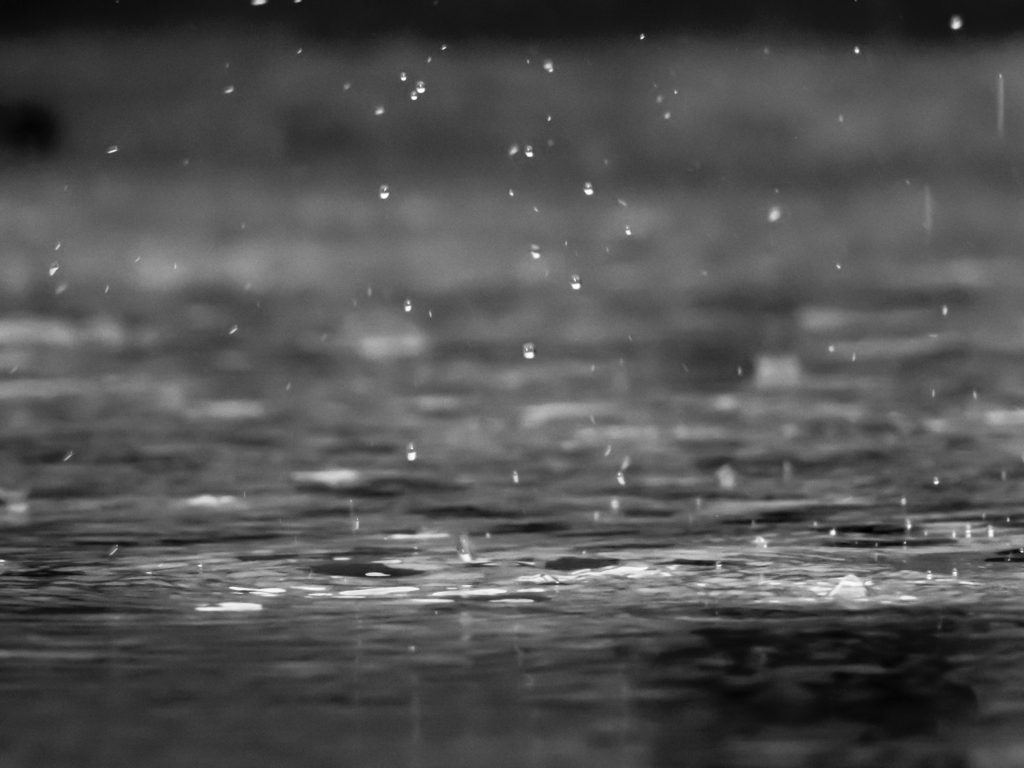
Direct rainwater collection systems typically intercept roof drain risers before they leave the building, with above- or below-ground storage tanks. Site stormwater runoff is typically collected through catch basins and site storm drainage located by paved parking surfaces. This kind of system must separate oils and grit before storage.
Things to consider when installing a rainwater harvesting system:
– The Phoenix area is a desert climate with limited rainfall (rainwater harvesting is supplemental, not primary and ROI may take years)
– Upfront and operating costs are attractive due to the simple system design
– Analyze annual rainfall vs. your building’s needs in relation to startup costs and local water costs
– Design systems that meet water goals
– Sized large enough to fill during rain events
– Overflow connected to stormwater draining system
– Connection to potable water system via break tank or phys air gap for supplemental water source
− Significant coordination between the plumbing and civil engineers is crucial for a coordinated system
– Rainwater harvesting systems benefit the building owner as well as municipalities with overburdened sewer systems during rain events
Pressure Reduction
High-rise and commercial buildings often require domestic water domestic water booster pumps to overcome pressure loss due to elevation increases in order to maintain water supply in water towers and other supply tanks. Such higher pressures mean water flows through the system at a greater flow rate and through terminal fixtures beyond rated flow capacities for those fixtures. Water used offers no additional benefit to the rated performance and is thus wasted.
By installing pressure-reducing valves, your water pressure is lowered to reduce water flow and use. Lowering the pressure also helps prevent rupture to pipes, and unnecessary damage to fixtures, which ends up wasting the water you were trying to save.
Insulate Piping
Insulate piping and storage tanks will be an energy code requirement for your new build. However, your existing building may have uninsulated or poorly insulated hot and hot water return piping. When hot water is needed, users will have to wait for fixtures to produce a hot water flow, thus wasting water while it takes time to heat up. Properly insulated return piping also means warmer water is supplied back to the hot water plant and reduces the energy demand to heat the water, likely resulting in less waste.
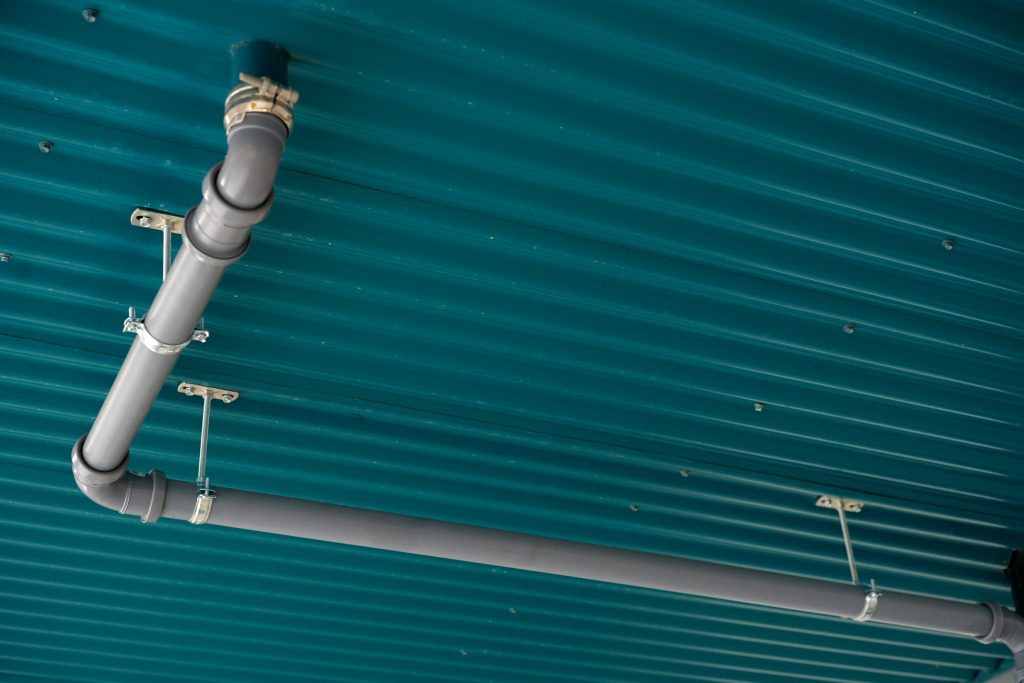
Leak Proofing or Repairing
Leaky pipes can go unnoticed, sometimes for months or years. Pipes are concealed out of sight, in every nook, cranny, crawlspace, and chase in the building, meaning leaks and water damage aren’t typically detected until visual damage, like water stains or puddles, are visible. Hopefully, your water audit located and identified these leaks and part of your water efficiency update is to fix them. Different types of damage affect water loss rates in varying significance. What seems like a minor dripping faucet or leaky toilet cistern can actually cost gallons of water loss per day.
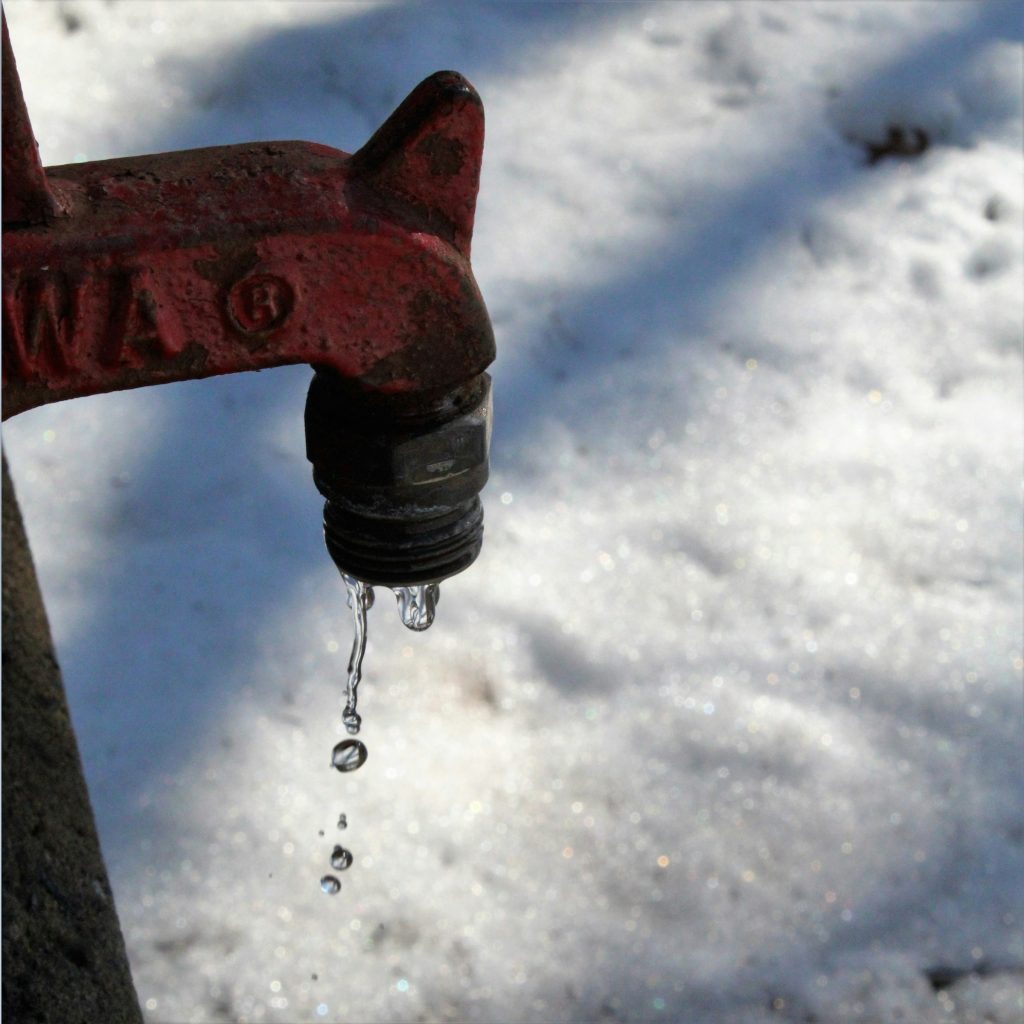
Things to consider when mitigating leak potential or repairing leaks:
– When installing a system, create a maintenance plan with proactive approaches and quick fixes to optimize water conservation
– Include design modifications to reduce or find leaks prior to waste and damage
– Include water monitoring through metering and sub-metering
– Add leak detection systems in critical or remote locations and tie them to a building automation system to notify maintenance staff of leaks to ensure quick response and prevent permanent damage to walls, ceilings, and equipment
– Install dedicated lines to high-usage areas to ensure point-of-use pressure is maintained
– Create isolation zones so users can shut down leaky pipes without interrupting whole-building usage
Irrigation Rain Sensors
Commercial or large properties with automatic irrigation systems program those systems to activate on a certain schedule. For instance, a system around a grassy area may be set to activate every Monday, Wednesday, and Saturday at 2 p.m. But if it’s raining on Wednesday between 1-5 p.m., that Wednesday watering really isn’t necessary. Depending on the amount of rainfall, the extra watering from the system could cause water-logging and other negative impacts on landscaping.
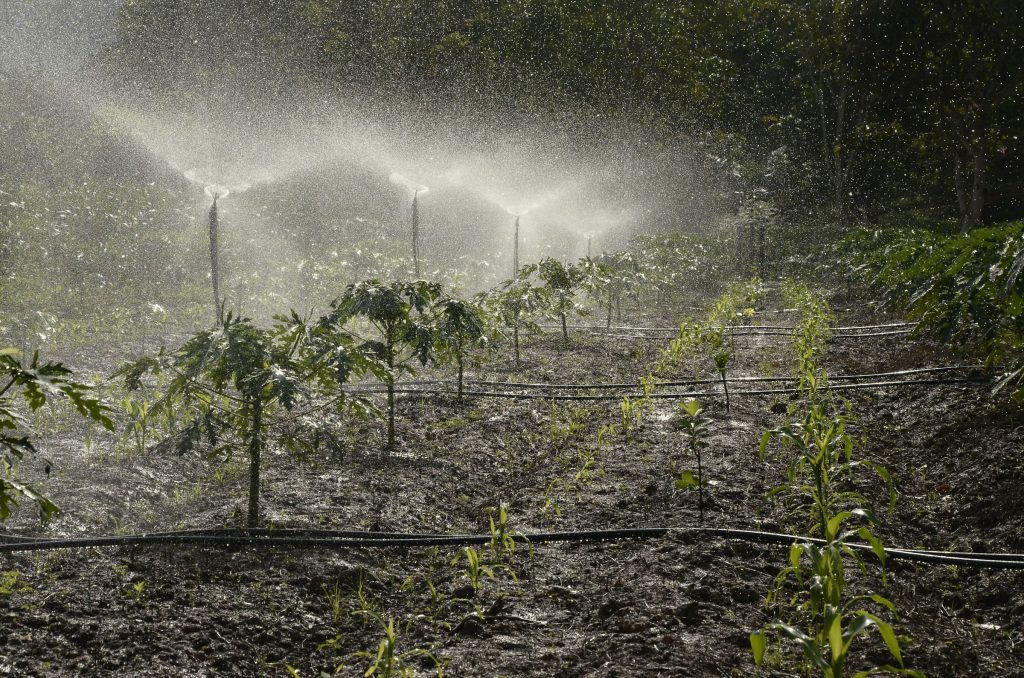
Installing a rain sensor on your irrigation system is a quick and easy way to conserve the water that would have been unnecessarily used by the system. Rain sensors are designed to identify when precipitation is present and lock out automated controls when the system isn’t needed. After the rain stops, the sensor resets and releases the controls so the system resumes without having to be reprogrammed.
Cooling Tower Water Recovery
Cooling towers remove heat from the building’s air conditioning system through evaporation of condenser water. All cooling towers continually through blowdown, drift, and evaporation, they consequently consume a significant percentage of a building’s total water usage. Blowdown is the removal of circulating water to maintain the amount of dissolved solids and other impurities at and acceptable level designated by the electrical conductivity of the water, and drift is water droplets that are carried out of the cooling tower with the exhaust air.
Towers in well-maintained, good conditioned, and properly operated towers allow chillers to operate at peak efficiency. Some can even use recycled water (stormwater or gray water) if the concentration ratio is maintained conservatively low. Blowdown water may be reused elsewhere on-site as well.
Things to consider when utilizing cooling tower water recovery:
– Evaporation is an integral piece of cooling tower performance and cannot be reduced without an acceptable reduction in performance
– Focus on drift and blowdown
– Blowdown reduced to minimum levels consistent with good operating practice can conserve significant amounts of water
– Treating condenser water by chemical means can reduce water loss
– Installing conductivity meters on blowdown lines reduces water usage during bleed/feed cycles
– Reduce drift and contain water treatment chemicals within the system to improve operating efficiency and reduce environmental impact with baffles or drift eliminators
In your new build, these improvements and modifications to the condenser water system should be implemented into installation at the design level to save you significant amounts of water from Day 1. Enacting a plan to minimize condenser water loss, ensure proper chemical levels, and constant regular system servicing all work together to save massive amounts of water.
Steam Boiler Blowdown
Boiler blowdown removes water from a boiler in order to control boiler water conditions within set limits to minimize carryover, corrosion, scale, and other specific problems. It is also used to remove suspended solids from the system, since poor quality feedwater will result in more frequent blowdown.
Things to consider when utilizing cooling tower water recovery:
– Use automated controls and treatment to reduce blowdown (less blowdown means more water saved)
– Update control equipment to prevent large fluctuations in blowdown, reducing water loss and energy used to heat water
– Variations in the rate of blowdown depend on feedwater characteristics, load on the boiler, and mechanical limitations
Educate Users
Water conservation isn’t just about “best practices” in design, but also informing and building an understanding among the consumers. This partnership helps achieve a greener and more energy-efficient built environment. It is important to educate your users about water scarcity issues, not only in Arizona but around the world, and the impact the above water conservation practices can have. Signage, point-of-use awareness campaigns, and publications targeted at consumers help spread the word about the benefits of water conservation, both in business and at home for the largest impact possible on an ever-dwindling natural resource: fresh water.
Final Thoughts
Conserving water doesn’t just reduce water waste, it reduced energy costs too, in operation and production. By utilizing current and future water conservation technologies in building and construction, we can help reduce the impact on an environment where water is a necessity of survival. Whether you’re building a new building or looking to retrofit an existing building for greener water usage, Realty Asset Advisors can help.
Contact us today!
0 Comments